At Banke Tradecom Services Pvt Ltd (BTS), we understand the importance of selecting the right type of steel for your construction projects. Whether you are working on a large infrastructure project or a residential building, choosing between CRS (Corrosion Resistant Steel) TMT bars and Epoxy-Coated TMT bars can greatly impact the longevity and integrity of your structure.
In this blog, we break down the differences between these two types of steel, helping you make an informed decision that suits your project’s specific requirements.
What is CRS TMT Bars ?
Full form of CRS Steel is Corrosion Resistant Steel. CRS TMT bars are designed with an alloy that includes elements such as chromium, copper, and phosphorus, which make them naturally resistant to corrosion without the need for any external coating. This makes CRS bars a reliable option for long-term durability in environments where moderate corrosion is a concern but where extreme conditions aren’t a primary factor.
- Applications: Ideal for residential buildings, dams, bridges, and infrastructure projects in environments with moderate corrosion risks, such as urban areas with occasional moisture exposure.
- Advantages:
- Long-lasting corrosion resistance due to the alloy composition.
- Low maintenance and high durability.
- Cost-efficient as no additional coatings are required.
- Disadvantages: Less suited for highly corrosive environments like coastal areas, as their natural corrosion resistance may not be enough for extreme conditions.
What is Epoxy-Coated TMT Bars?
Epoxy-coated TMT bars are produced by applying an additional layer of epoxy over standard steel bars. This epoxy coating acts as a protective barrier against corrosion, especially in environments where the steel is exposed to harsh chemicals, saltwater, or moisture. While more expensive than CRS TMT bars, epoxy-coated bars offer exceptional corrosion protection.
- Applications: Perfect for marine structures, bridges, piers, ports, coastal infrastructure, and areas with high humidity or chemical exposure.
- Advantages:
- Provides a superior barrier against corrosion in highly corrosive environments.
- Offers extended service life in conditions that would otherwise accelerate corrosion, such as marine or chemical exposure.
- Great for use in coastal areas or where exposure to de-icing salts is frequent.
- Disadvantages:
- Higher upfront costs due to the coating process.
- Risk of damage during transport and installation—if the epoxy layer gets scratched or chipped, the steel underneath can corrode faster.
- Coating may not withstand the rough handling common in some construction environments.
Comparisons Between CRS and Epoxy-Coated TMT Bars
- Corrosion Resistance:
- CRS TMT Bars: Corrosion resistance is built into the alloy through elements like copper and chromium. This provides inherent protection but is limited in extremely corrosive environments.
- Epoxy-Coated TMT Bars: Corrosion protection is achieved through an external epoxy coating, making these bars more suitable for highly corrosive settings, such as marine environments.
- Durability:
- CRS TMT Bars: Since there is no external coating, CRS bars are less likely to suffer damage during transport or installation. However, their corrosion resistance is moderate, so they are not ideal for coastal or chemical-exposed areas.
- Epoxy-Coated TMT Bars: The external coating provides excellent corrosion resistance, but it can be prone to damage during transport or rough handling. If the coating is compromised, it reduces the overall effectiveness.
- Cost:
- CRS TMT Bars: Generally more cost-effective than epoxy-coated bars due to the absence of an additional coating process. Ideal for moderately corrosive environments.
- Epoxy-Coated TMT Bars: More expensive due to the coating process and additional corrosion protection, but worth the investment for highly corrosive environments to ensure the structure’s longevity.
- Maintenance & Handling:
- CRS TMT Bars: Minimal maintenance required, with no concern about coating damage.
- Epoxy-Coated TMT Bars: Requires careful handling to avoid damage to the epoxy layer, and repairs might be necessary if the coating is compromised during installation.
- Suitability for Environment:
- CRS TMT Bars: Suitable for general construction projects where the risk of corrosion is moderate. Not recommended for environments with heavy saltwater or chemical exposure.
- Epoxy-Coated TMT Bars: Specifically designed for extreme environments with high moisture, salt, and chemical exposure, such as coastal and marine structures.
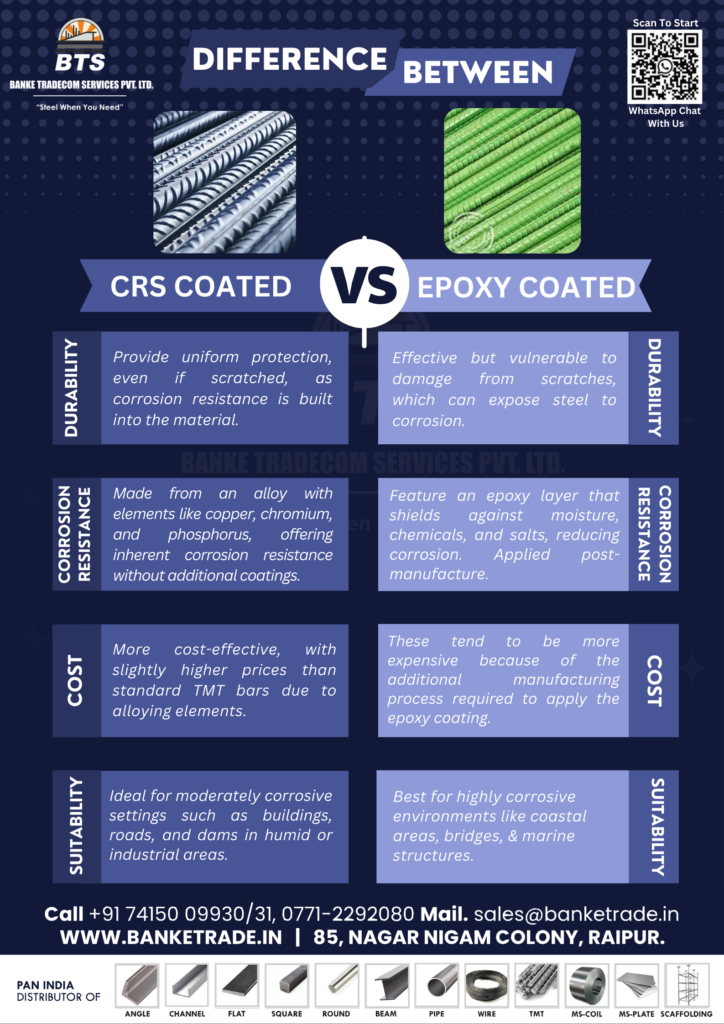
Is Epoxy-Coated Rebar Better?
Whether epoxy-coated rebar is the better option depends on the environment and the project’s specific requirements. Epoxy-coated TMT bars offer exceptional corrosion resistance in harsh environments where standard steel or CRS TMT bars might corrode quickly. In areas with high salt content, moisture, or chemical exposure, epoxy-coated bars are essential for ensuring the longevity of the structure.
However, for projects located in less corrosive environments, CRS TMT bars offer a more cost-effective solution without the risks associated with coating damage during handling. So, while epoxy-coated rebar is “better” for high-risk corrosion environments, it may not be the most economical or necessary choice for all projects.
Why the Right Choice Matters
The choice between CRS and Epoxy-Coated TMT bars significantly impacts the long-term durability, safety, and cost-efficiency of your project. CRS TMT bars offer reliable corrosion resistance for general construction, while epoxy-coated bars are indispensable for projects in highly corrosive environments.
Why Choose BTS?
At BTS, we provide both CRS and Epoxy-Coated TMT Bars, allowing you to select the right material based on your project’s environmental and structural needs. With our commitment to quality and timely delivery, we ensure that you get the best material for long-lasting and durable construction projects.
Get in Touch Today for Your Steel Needs!
Looking for a trusted steel supplier in Raipur CG? Contact BTS for high-quality steel products and expert service. We’re here to support your project from start to finish.
📍 Location: Raipur (CG)
📞 Phone: 07712292080 | 07415009930 | 07415009931
✉️ Email: sales@banketrade.in | steel@banketrade.in
🌐 Website: www.banketrade.in
Stay Connected with Us on